By definition, a primer comes first and serves as a base for what should follow — whether it’s attending the primary grades at the beginning of school, priming an engine to start or using a primer coat applied prior to painting a wall. Similarly in commercial roofing, a primer is used as the first step in the application of a roof coating or membrane to aid in the proper bonding of the product to the surface.
Roof primers come in many different forms; so the type of primer used depends on some key circumstances, including the substrate, the weather conditions and the type of coating or membrane application. Surfaces that require primer include concrete and masonry roof decks, and gypsum, block, brick, parapet walls and metal flashings. Priming the surface can be a critical step and is important for the best possible adhesion. More importantly, the better the contact with the substrate, the better the primer’s performance.1
With this necessary information, a number of questions may come to mind, including, “Why do I need a primer?” A fair question, and thus, the purpose of this article — to help you make an informed decision about an essential part of the roofing and reroofing process. Keep in mind that this article will focus on primers as they pertain to asphalt membrane applications, and more detail on the aforementioned circumstances follow below.
What is an asphalt primer made of and how do its penetrating qualities help promote adhesion and ensure a firm, tough bond?
Standard asphalt, mod bit and spray primers are solvent-based and intended to prepare roofing and wall surfaces prior to applying heat-welded membranes. These primers are formulated with a rubber-modified bitumen and fast-evapourating solvents for quick drying, and enhanced membrane adhesion to a variety of substrates, such as gypsum, masonry, metal or concrete. This improves membrane performance over a wide range of temperatures and conditions.2
Generally, decisions about primer applications should not be made without consulting manufacturer requirements for the specific coating or substrate. A primer is never a substitute for proper roof coating or membrane preparation, as the substrate should be clean and dry before application. An essential first step before application is a quick inspection for debris, followed by necessary cleaning, as any surface containing dust or dirt will compromise the bond.
Some substrates require an asphalt-based primer prior to the application of the membrane product. Specifically, only asphalt primers should be used with asphalt materials, such as modified bitumen products. And while primers work best on clean and dry surfaces, asphalt emulsions primers can be applied to damp but not wet surfaces. Additionally, primer and surface coating or membrane applications should occur in rapid succession. Again, check manufacturer recommendations before using a primer.
The Roof Coatings Manufacturers Association (RCMA) recommends a few general guidelines regarding the application of primers. Asphalt roofs, such as built-up roofing (BUR), styrene-butadiene-styrene (SBS) and atactic polypropylene (APP) systems or modified bitumen membranes and granulated cap sheets, contain light oils, or exudate, that can leave a membrane soon after its application. This process, called “tobacco juicing,” is normal, and the exudate will generally wash off the roof after rainstorms. Any exudate on a roof prior to coating application should be thoroughly cleaned. As with any substrate, if in doubt, perform a test patch to ensure proper adhesion of the primer.
Weather Conditions
The application of all roofing systems during cold weather poses special concerns. The Asphalt Roofing Manufacturers Association (ARMA) prepared a technical bulletin to address cold weather applications. Specific to modified bitumen materials, these concerns may include maintaining proper asphalt, primer, adhesive and sheet material temperatures at the point of application. Cold weather may reduce the curing rate of solvent-based adhesives, cause mopping asphalts to harden prematurely, stiffen sheet materials and reduce the effectiveness of self-adhesive materials. By following proper procedures and exercising recommended precautions, cold weather application can progress more efficiently and effectively, so that a higher-quality result can be attained.3
Industry Standards and Guidelines
ASTM (formerly American Society for Testing and Materials) is a not-for-profit voluntary standards developing organization that develops and publishes voluntary consensus standards for materials, products, systems and services. These standards are highly regarded, and they help to specify, test and assess the physical, mechanical and chemical properties of products. The standards also help determine that the products will perform as specified and are safe for use.
“ASTM D41 is the Standard Specification for Asphalt Primer Used in Roofing, Dampproofing, and Waterproofing. This specification covers asphaltic primer suitable for use with asphalt in roofing, dampproofing, and waterproofing below or above ground level, for application to concrete, masonry, metal, and asphalt surfaces. Asphalt primer shall be classified as Type I and Type II. To determine the properties of the asphalt primer, the following test methods shall be performed: furol viscosity; distillation; penetration; and matter soluble in trichloroethylene.” More information on ASTM D41 is available on the ASTM website.4
What are VOCs and Why are They Important When Considering a Primer?
Volatile organic compounds or VOCs have been a concern for decades, both in North America and across the world. Organic chemical compounds are everywhere in both indoor and outdoor environments because they have become essential ingredients in many products and materials. VOCs are an ongoing consideration throughout the commercial roofing industry, from single-ply, to coatings and asphalt roofing membranes.
Many state/provincial and municipal building codes regulate the use of materials that include VOCs to reduce the likelihood for future health-related issues and sustainability. As VOC regulations have tightened over the years, asphalt roofing products have kept pace.5 Asphalt roofing products, and the coatings and adhesives used in the installation and maintenance of asphalt roof systems continue to provide long-term performance on the roof while achieving compliance with the wide variety of VOC regulations that exist throughout the U.S. and Canada.6
In their website article discussing a regulatory overview of VOCs, Underwriters Laboratories (UL) cites VOCs as chemicals that vaporize at room temperature and states that they are the leading cause of ground-level air pollution, also known as smog.
The web post notes that VOCs react with nitrogen oxides — particularly on hot summer days — to form smog. Common sources of VOC emissions include car exhaust, gasoline-powered lawn and garden equipment, gas stations, industrial coatings, paints, household chemicals and building/furnishing materials.
In sufficient quantities, VOCs can cause eye, nose and throat irritations, headaches, dizziness, visual disorders and memory impairment. In more extreme cases, some are known to cause cancer in animals, and some are suspected of causing cancer in humans. Since the volatility of a compound is generally higher the lower its boiling point temperature, the volatility of organic compounds is sometimes defined and classified by their boiling points.
As an example, the post also cites how the European Union uses the boiling point, rather than its volatility in its definition of VOCs. A VOC is any organic compound having an initial boiling point less than or equal to 250 C measured at a standard atmospheric pressure of 101.3 kilopascals (kPa).
The higher the volatility (lower the boiling point), the more likely the compound will be emitted from a product or surface into the air. Very volatile organic compounds are so volatile that they are difficult to measure and are found almost entirely as gases in the air rather than in materials or on surfaces. The least volatile compounds found in air constitute a far smaller fraction of the total present indoors, while the majority will be in solids or liquids that contain them or on surfaces, including dust, furnishings and building materials.7
U.S. patents related to low VOC asphalt primers are abundant, with interesting data related explicitly to the topic in detail on the Google Patents website. For even more information
on VOCs, take a look at the information about the subject on the U.S. Environmental Protection Agency’s website.
Types of Asphalt Primer Applications
Asphalt primers may be applied in several ways — by roller or brush, with a sprayer or from an aerosol can. Commercial roofing manufacturers, such as IKO, offer a number of options for the application of their asphalt primer products.
IKO Mod Bit Primer is solvent-based and intended to prepare roofing and wall surfaces prior to applying heat-welded membranes. IKO Mod Bit Primer is formulated with a rubber-modified bitumen and fast-evapourating solvents for quick drying. The modified bitumen enhances membrane adhesion to a variety of substrates, such as gypsum, masonry, metal or concrete, and it improves membrane performance over a wide range of temperatures and conditions. IKO Mod Bit Primer can be applied with a brush, roller or sprayer.
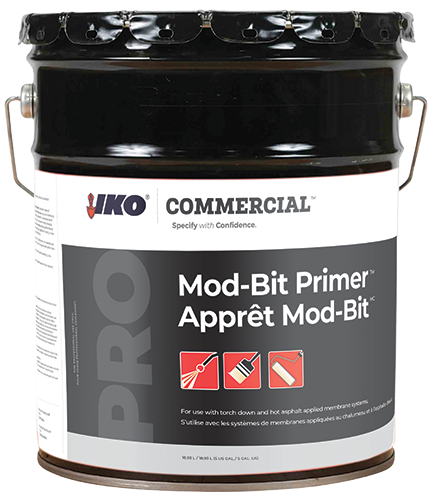
IKO Standard Asphalt Primer is intended for use prior to the application of hot asphalt, some fibrated asphalt coatings, asphalt emulsions or asphalt adhesives. It is used as a one-coat application when fast drying is needed to accelerate the roof system installation process. IKO Standard Asphalt Primer promotes adhesion and may be used to prime and/or seal gypsum, masonry, metal, wood, concrete, asphalt and other similar substrates.
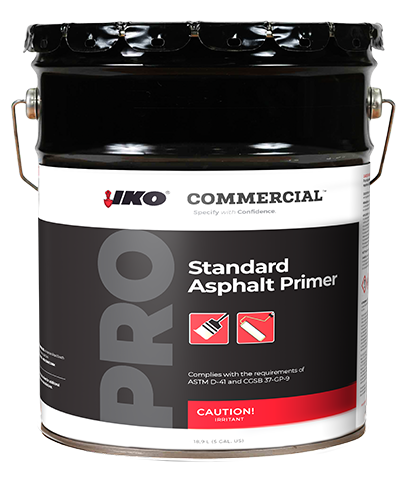
IKO Spray Primer is a high-quality asphalt-based primer in an aerosol can. It may be used as a single coat when fast drying is needed to accelerate the roof system installation process. IKO Spray Primer is excellent for priming and sealing porous surfaces to improve the bonding of asphalt-based materials and also can be used as a corrosion-resistant coating for metal. IKO Spray Primer is a versatile, one-coat application product and may be used to prime and/or seal gypsum, masonry, metal, wood, concrete, asphalt and other similar substrates in small detail areas.
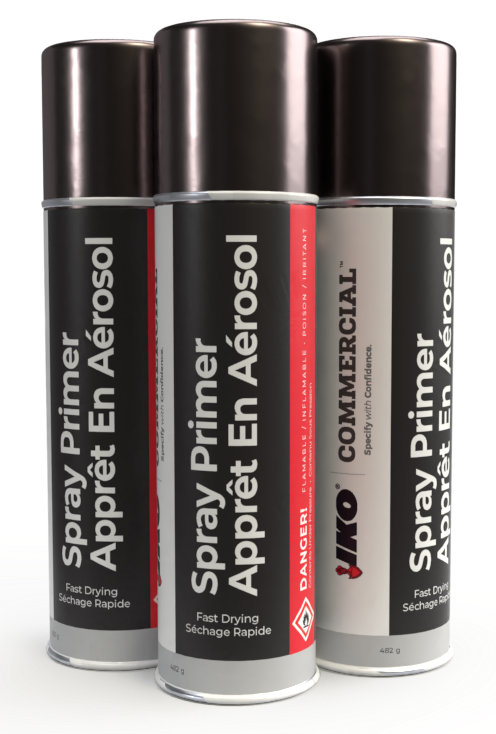
As you now consider your next asphalt commercial roofing application, we hope you recognize what an important role a primer can play in the success of installing an outstanding commercial roofing system. For more information on how to become an IKO commercial installer, please visit IKO’s Request Contractor Training.
References:
1, 3 Roof Coating Manufacturers Association (RCMA).
2 IKO.
4 ASTM.
5 Asphalt Roofing Manufacturers Association (ARMA).
6 Environment and Climate Change Canada.
7 Underwriters Laboratories (UL).