If You’ve Ever Wondered “What Are Shingles Made of?” IKO Roofing Has the Answer
Your home is an investment. Protecting your home is very important. A roof goes on to your home and putting something on your home that’s going to last is very important. It protects your loved ones, it protects your most precious and valuable things that you have inside your home and it adds beauty to your home.
Today we’re at an IKO manufacturing facility, we’re going to be doing a lot of quality testing to ensure that our shingles are the best quality roof shingles. So, we have SOPs in place, which is Standard Operating Procedures, and that makes sure that every facility is doing the same amount of testing, and also the same equipment is used. Every IKO plant has a lab facility. We can check the quality of our shingles every hour, every shift, to make sure that from the beginning of making a shingle to the very end of the shingle complies with roof quality assurance. We check everything that comes in from the door. Each area on the line has shingle quality checks as well, so we’re ensuring from the time the fiberglass roll is put onto the line, to the time it’s wrapped, to the time actually it’s put onto a truck, that it meets our quality standard guideline. We put a lot of time, a lot of work, a lot of care into making this product. A lot of people have no idea what it takes to actually make and keep the product up to standard. But we do it, and we’re going to make sure that IKO looks really good on your house. I can ride by in a car and I can say “”oh wow that looks like a Dynasty! That’s a Cambridge, or we make that!”” I can look at a shingle and tell that I put my hands on it.
Asphalt Dominates
Asphalt shingles remain the dominant roofing option in North America, and they are found on roofs in scores of countries around the world. Regardless of color or style, they are all manufactured in basically the same way in a continuous web process, using a short list of key raw materials. So what exactly goes into an asphalt roofing shingle anyway?
1. Fiberglass
As mentioned, the manufacturing process uses a continuous web or sheet which provides the foundation upon which the asphalt and other materials are applied. Asphalt roofing shingles are reinforced with a thin fiberglass mat, made from glass fibers of specific length and diameter bound together with the help of stable resins and binders. The fiberglass is wound into large rolls at the fiberglass mill, which are then “unwound” at the start of the roofing shingle manufacturing process.
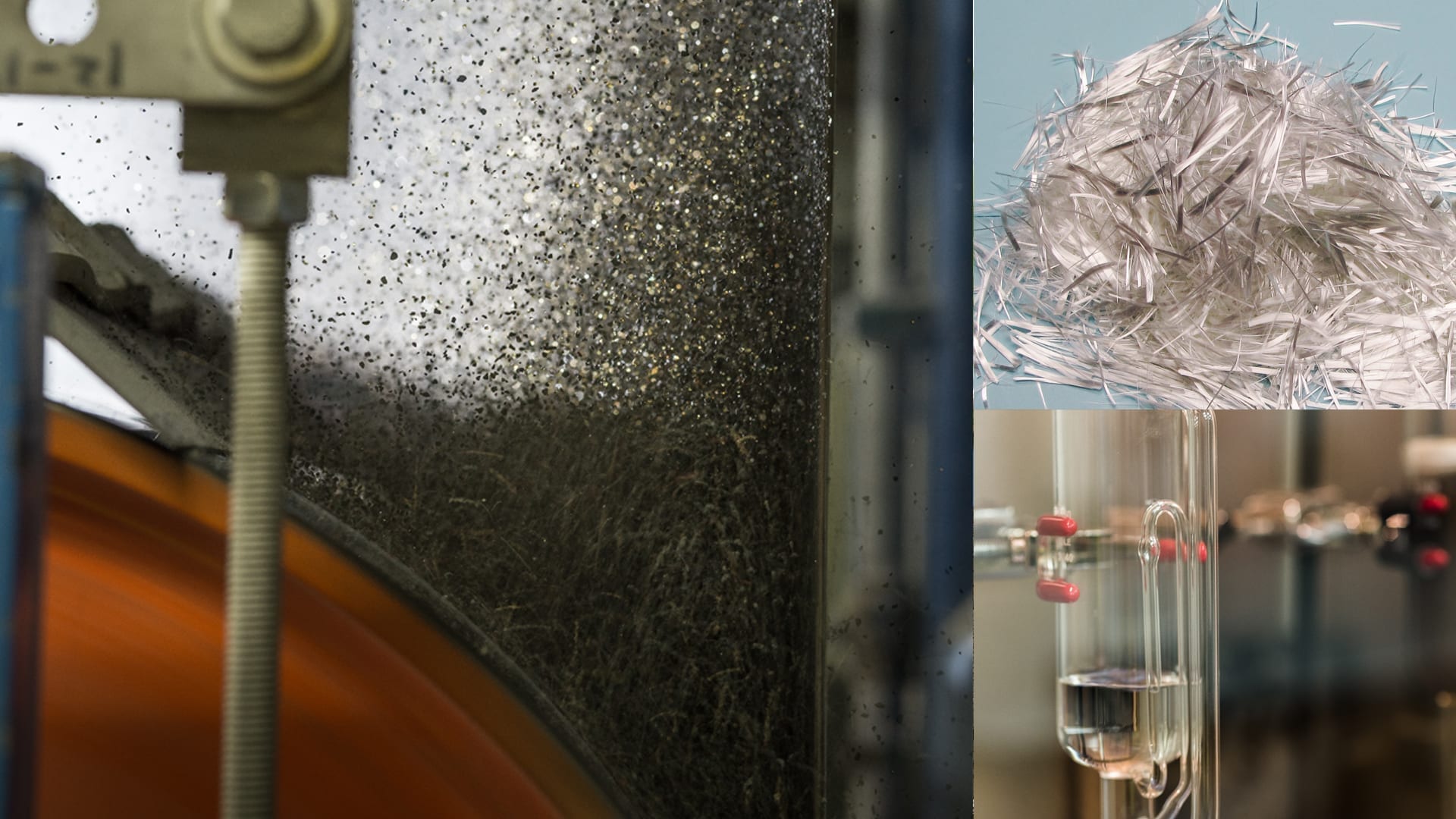
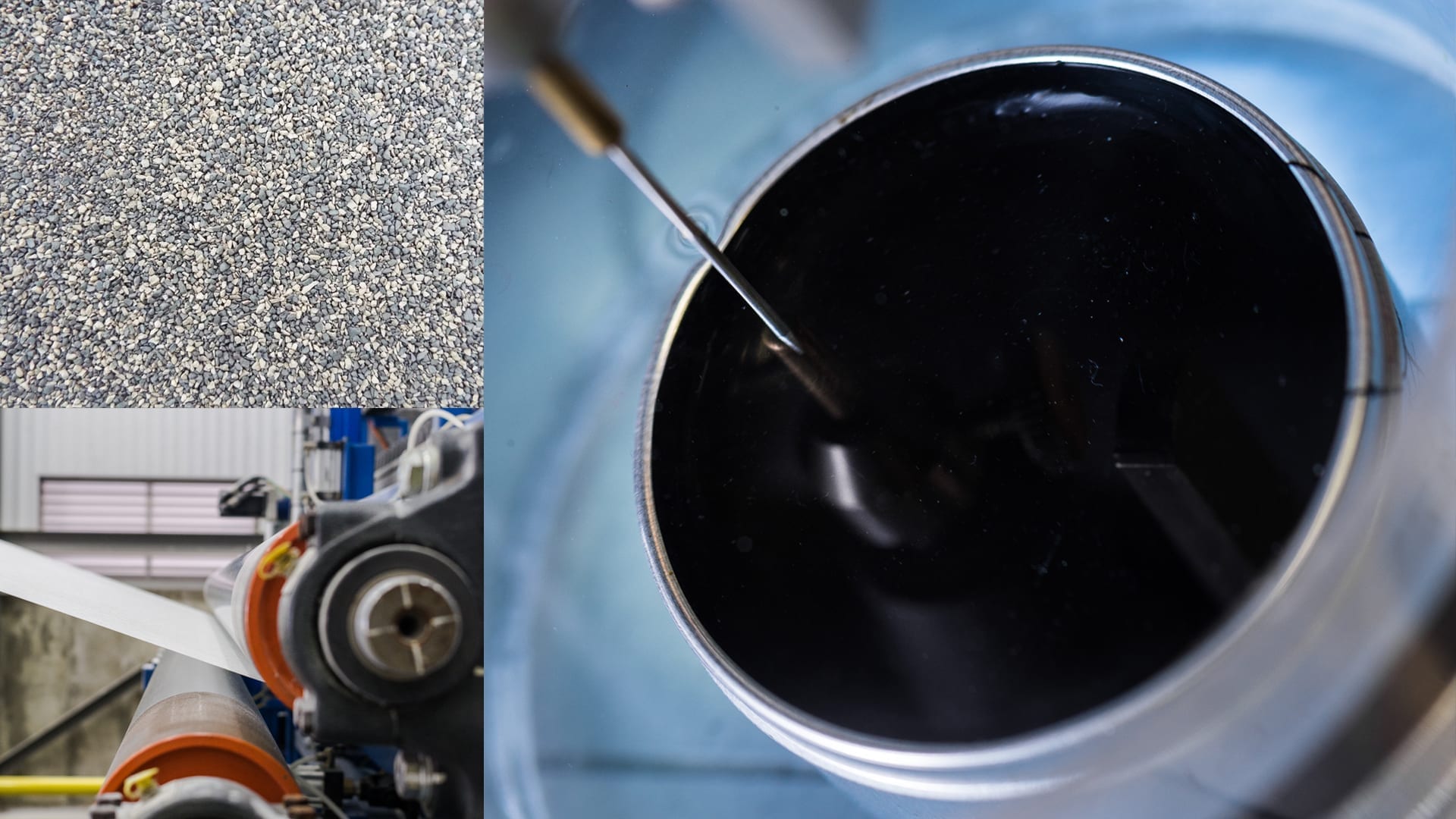
2. Asphalt
Asphalt is the main water-resistant ingredient in shingles. The asphalt used is an end-product of oil refining and, although somewhat similar in origin to road asphalt, it is processed to a higher degree of toughness needed for asphalt shingle performance. The roofing asphalt has to be “oxidized” by blowing air through the hot asphalt, increasing its viscosity. But the air blowing process must be precise – too much and the shingles can be brittle, too little and the shingles may be too soft and prone to scuffing if installed in hot weather. A fine mineral powder is mixed with the asphalt to increase weather resistance and enable the installed shingle layer to meet the highest standards for resistance to fire hazards. The mineral-fortified asphalt “coating” is applied to the fiberglass mat on top and bottom.
3. Granules
The most visible aspect of asphalt roofing shingles is the stone granule surfacing. Hard rock with certain physical properties is crushed and screened to exact granular size specifications. In the part of the shingle not exposed to view, the granules are applied as is, in their natural stone-colored state. The granules (sometimes referred to as ‘grit’) are processed into a variety of colors via ceramic firing to give them the long-lasting colors used on the exposed part of the shingle. Some shingles feature an algae-resistant granule that helps inhibit discoloration caused by blue-green algae. As well, special “reflective” granules can be used to make roofing shingles that reflect a higher percentage of the sun’s heat energy. Such shingles are required by code in certain regions.
Close-up of ceramic granules, a critical part of what shingles are made of.
4. Sealant
To bond the shingles together on the roof, spots of a thermally-activated asphalt sealant are applied to the shingles (some shingles have the sealant positioned on the top surface, while on other shingles, the sealant is located on the bottom). If the shingles are multi-layer laminated shingles, like most shingles installed today, a similar material called laminant is used to adhere the shingle layers together at time of manufacture. The top layer of a typical laminated fiberglass shingle is called the dragon tooth as it simulates an exaggerated tooth appearance; the bottom layer is called the shim. These asphaltic adhesives are specially engineered to ensure they activate at the desired temperature ranges and hold their bond through the rigorous shingle installation process in the case of laminant, and also during wind events and other roof stresses.
Mike Anderson, Manager of Quality Assurance, Research and Development at IKO Industries states, “Although a very small weight contribution to the shingles, sealant and laminating adhesives are critical to the performance of the shingle, and hence the overall installed roof system. This is why IKO continues to devote significant and on-going research efforts to ensure its sealant and laminating adhesives are designed for optimal strength. Each IKO shingle manufacturing facility processes its own adhesives on-site to a controlled recipe that ensures maximum adhesion under the broadest temperature range IKO shingles are designed to comply at the time of manufacture with the highest industry standards.”
Since the asphalt coating on the roofing shingle is itself a sticky material, the bottom side of the product needs to be covered with something to keep the shingles from sticking to the process rolls during manufacturing, and from sticking together in the package. In the roofing industry, this material is known as backsurfacing. If you look at the back of an asphalt shingle, you can easily see what it is – a fine mineral powder, often sourced from limestone-type rock or fine sand.
5. Release Film
The final asphalt roofing shingle component is one that used to cause a bit of confusion in the amateur roofing community. Mentioned above are the small spots of asphalt sealant that, with sufficient solar heat, will bond the shingles together. When shingle bundles are stored outside in summer or in a hot warehouse, what keeps the sealant from premature activation and sticking all the shingles together right in the package? A material called “release film”. It looks like a shiny plastic tape about an inch or so wide, most often located on the back of the shingles. The release film does its job only while the shingles are in the package. Once they’re installed, the film serves no purpose at all and just stays on the back of the shingle. However, if it’s peeled back (often not so easy to do since it is not designed to be removed), naturally the shingle coating asphalt underneath looks black and shiny, and is a bit sticky. And so, for many years, some rookie installers thought peeling off the release film exposed sealant that was needed for shingle adhesion on the roof, but that’s simply not true.
So, although there is a short list of raw materials in asphalt roofing shingles, each serves a key purpose. They are selected, processed and designed to work together to make a roofing material that is, weight for weight, among the best value options available.
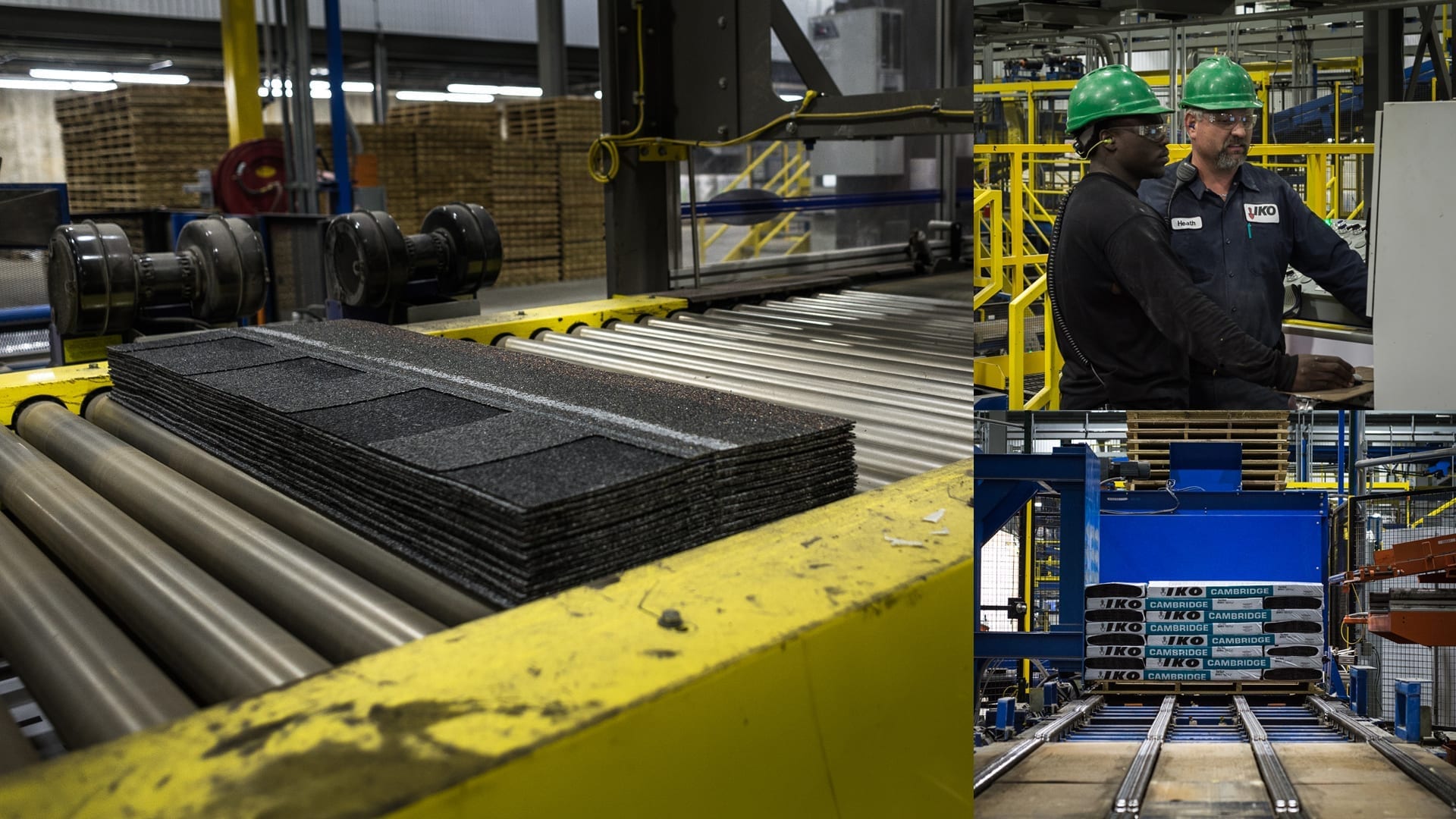
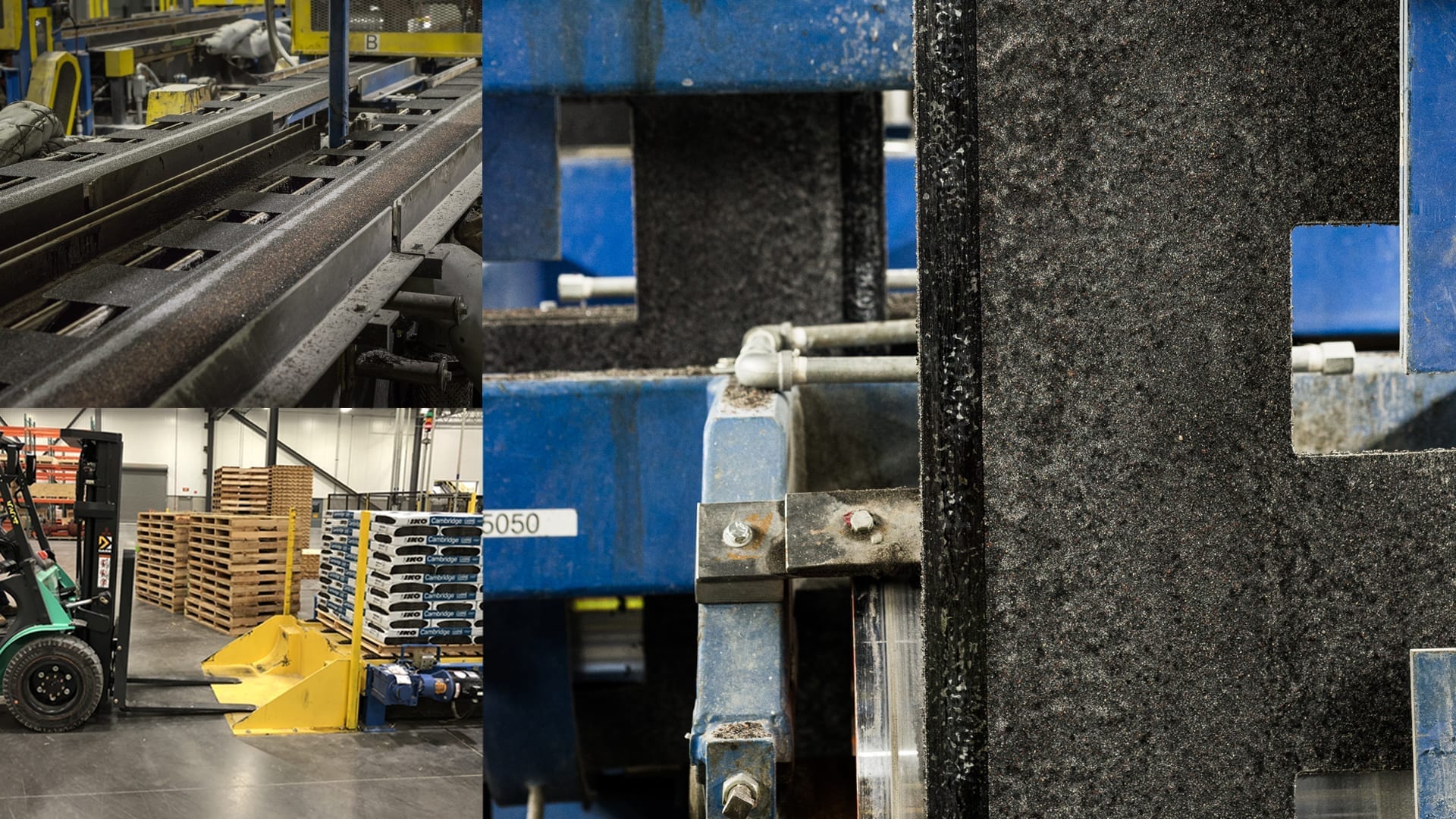