A Design & Materials Guide for Residential Flat Roofing Systems
TABLE OF CONTENTS:
- Flat Roofs Are Everywhere–But What About Homes?
- Why Are Flat Roofs Less Common For Houses?
- Flat Roof Drain Types
- It Looks Good
- Flat Roof Space Is Usable Space
- It Performs and Protects Well
- Examining Flat Roof Myths–What Are The Drawbacks?
- Parts Of A Flat Roof
- Other Flat Roof Components
- Warm vs. Cold Roofs
- Flat Roof Designs For Houses
- Built Up Roofing (BUR)
- Single Ply Membranes
- Thermoset (Synthetic Rubber)
- Thermoplastic
- Modified Bitumen (or Polymer Modified Bituminous Materials)
- Liquid Applied Roofing
- Spray On Roofing
- Metal Roofing
- Can you have a flat roof with shingles?
- How to Make a Flat Roof Last
- A crowning feature
Flat Roofs Are Everywhere – But What About Homes?
Flat roofs are a familiar sight throughout North America. Any typical mall, warehouse, apartment building or school usually features a flat roof. This roof type is easier to install over large surfaces and is the most common choice for commercial, industrial and institutional buildings.
From the start, you’ll likely have questions, including: is a flat roof the right choice for a home? Is it more expensive that a steeper pitched alternative? Is it harder to install? What about ongoing maintenance?
Whether choosing a roof design for a new home, or replacing/repairing a current flat roof, IKO Industries offers much of the information needed to make informed decisions for a lasting, sturdy cover for your investment. Explore the following guide to answer many of your flat roof-related questions:
Why Are Flat Roofs Less Common For Houses?
Also known as low slope roofs, flat roofs are less common in North American residential construction because the low slope of a flat roof has an increased tendency to collect water rather than shed, like its more steeply pitched alternative. This may make it less ideal for rainy or snowy climates.
Keep in mind, all flat roofs have a slope of between five and 15 degrees to allow water to flow into drain systems (such as eaves, drainage holes or outlets).
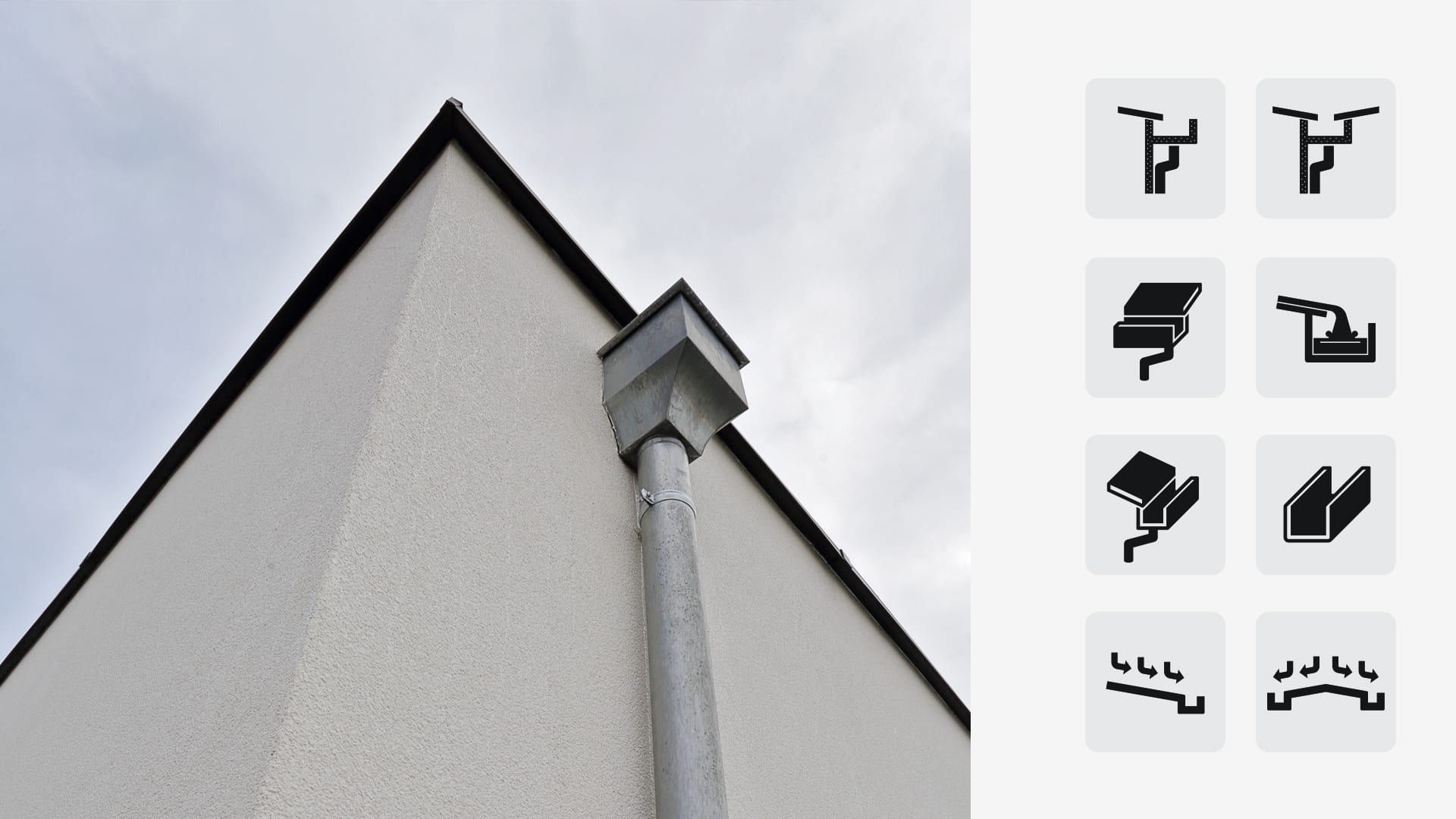
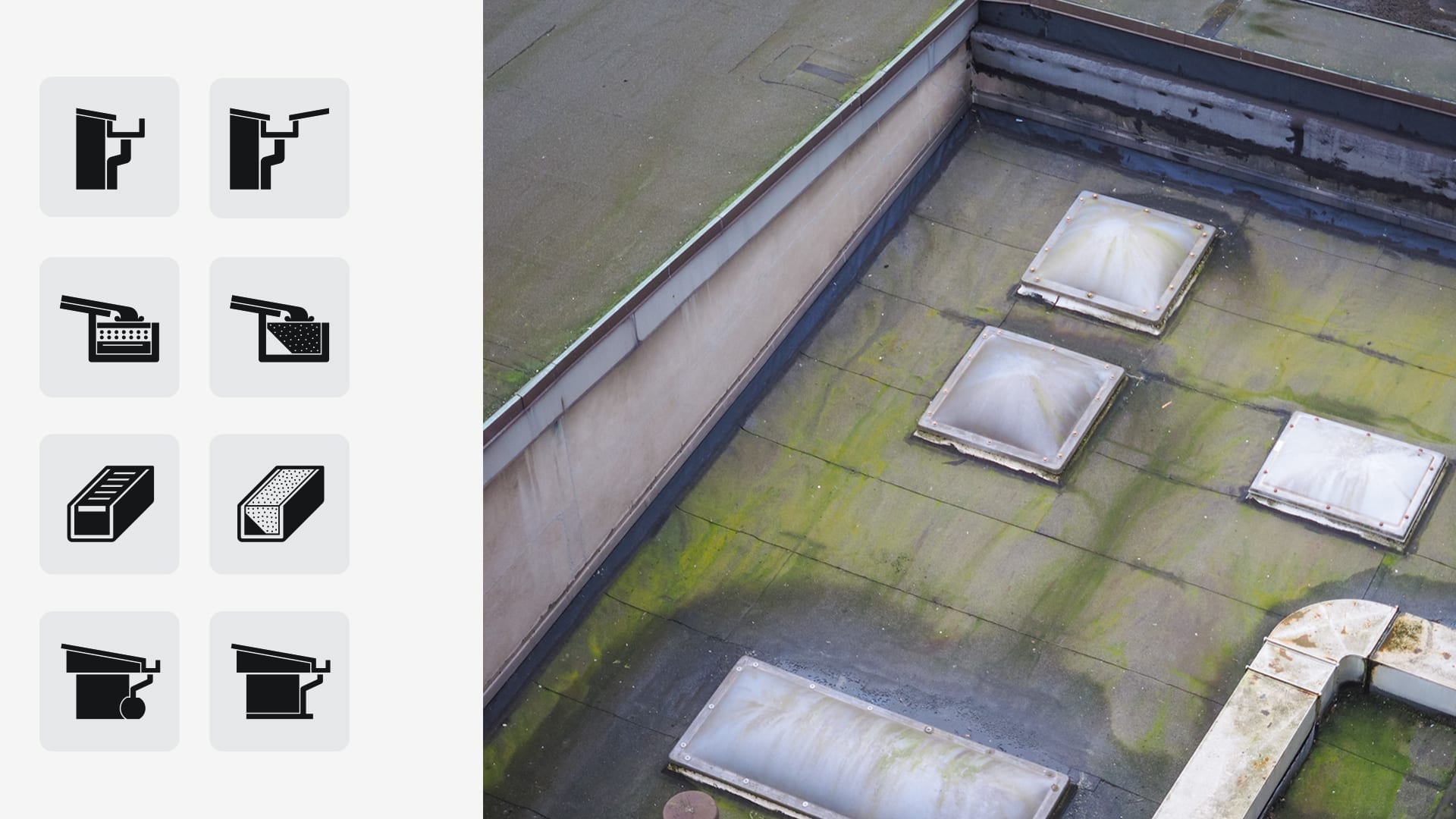
Flat Roof Drain Types
So, even though flat roofs are ideal for drier landscapes, in climates with heavy precipitation, a properly installed flat roof can be a fine choice for a homeowner – especially thanks to ever-improving waterproof materials and installation techniques.
It looks good
Flat roofs are an attractive aesthetic choice that give homes a unique form. If you love the landscape or cityscape around your home, a flat roof can help complement that without obscuring the view.
Flat Roof Space Is Usable Space
Unlike a steeply pitched roof, most of the square footage of a flat roof is available for use. This offers the option to add a unique application such as a rooftop patio, garden or green roof. Solar panels also are popular among homeowners and are much easier to install – and hide from view – on a flat roof.
Any of these applications will require certain design considerations (such as adding guardrails and other safety protections and/or using more heavy duty materials to handle roof traffic and weight). Special permits may be required from the local building authority, but these efforts may result in an entirely new feature to enjoy on your home.
It Performs And Protects Well
Flat roofs are a cost-effective option for homes – thanks to generations of use in commercial flat roof construction, modern materials and application techniques – as viable, protective and long-lasting alternatives to pitched roof counterparts.
By choosing the proper materials, hiring an experienced professional to build and install the flat roof, and committing to regular inspection and maintenance, homeowners may count on many years of reliable performance when selecting a flat roof solution.
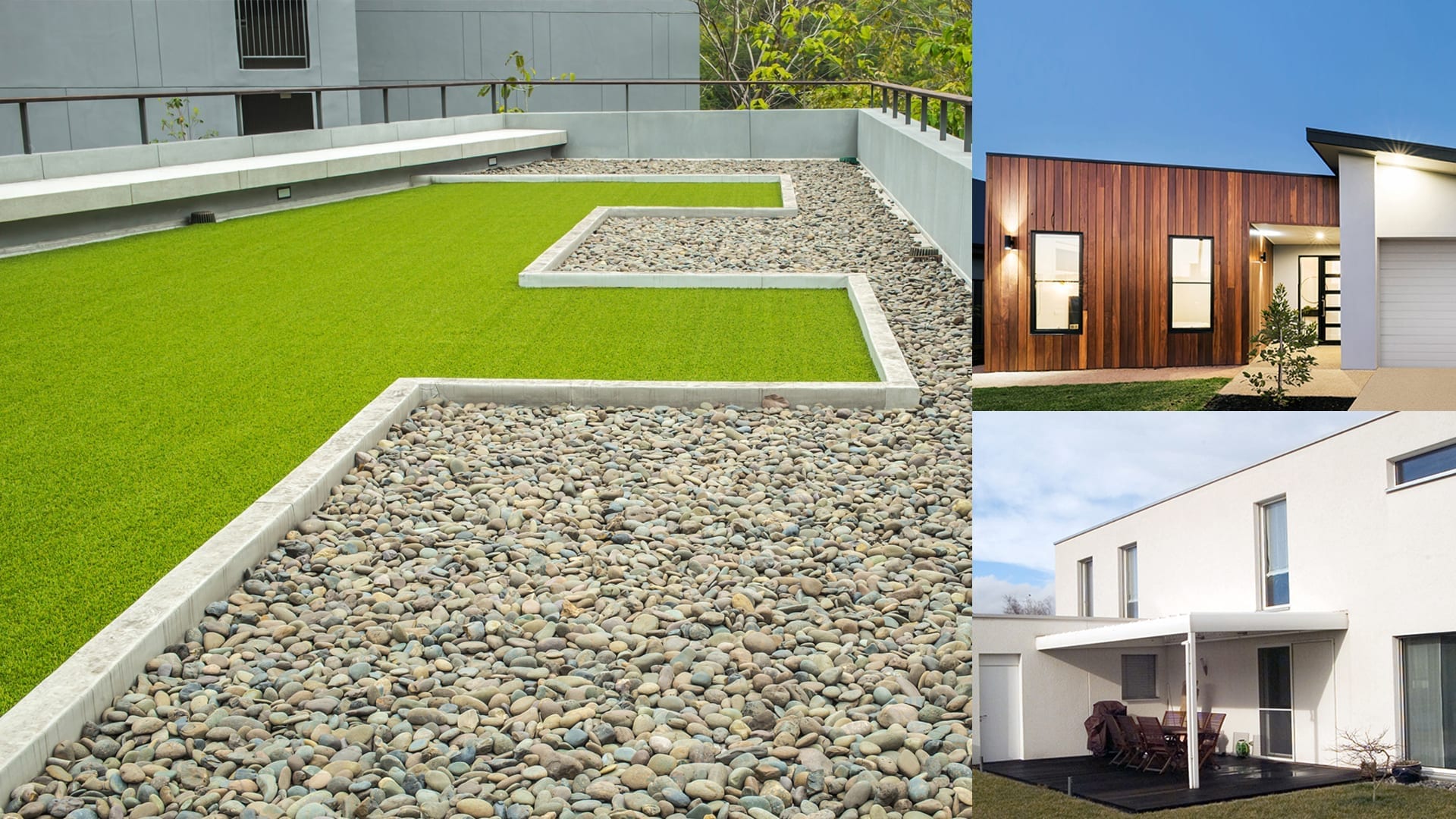
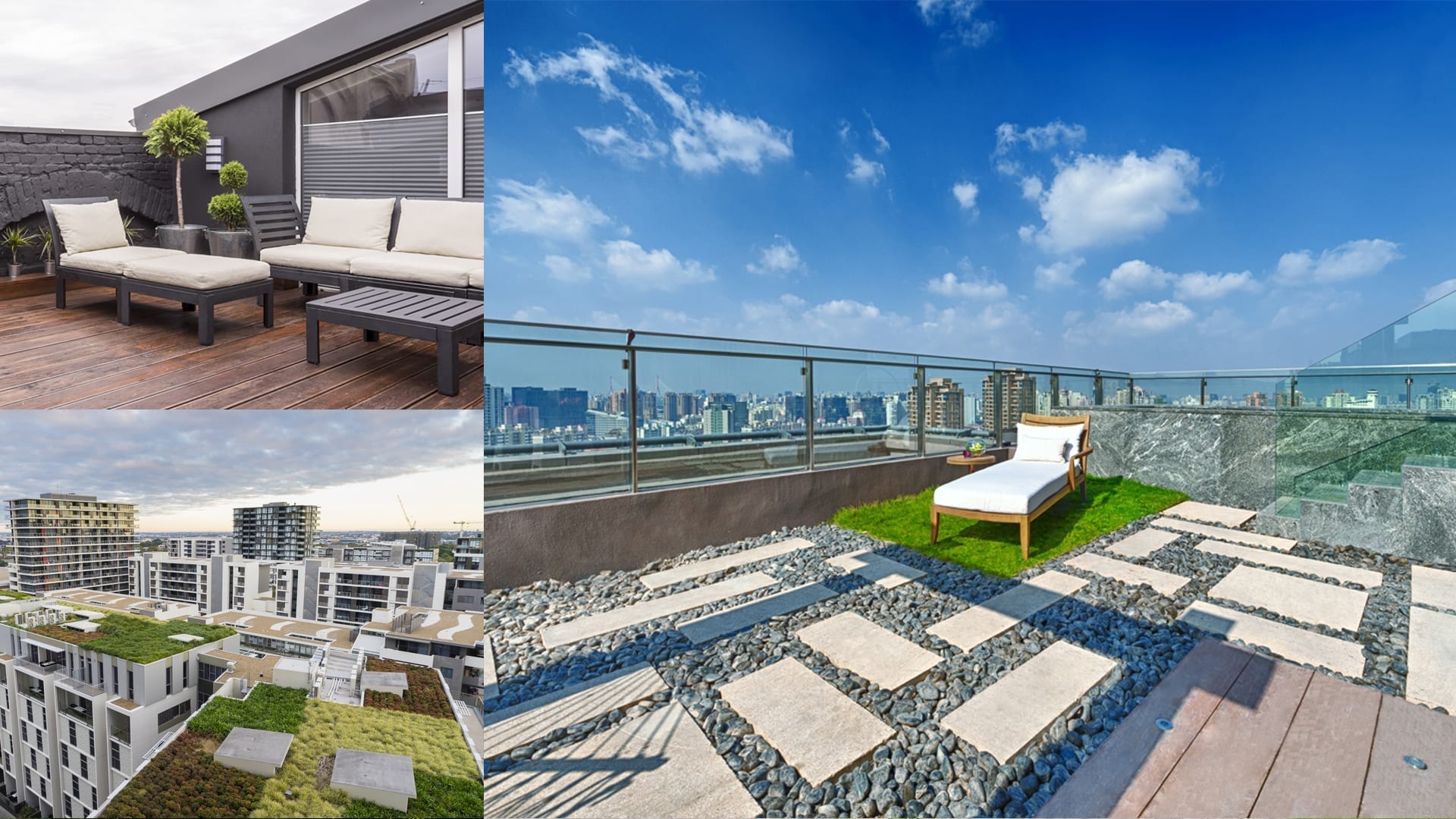
Examining Flat Roof Myths – What Are The Drawbacks?
Flat roofs are hard to replace
Some observers suggest it’s harder to replace a flat roof than a traditional pitched shingle roof because of the labor required to remove its layers (especially on older flat roofs). But now, flat roofs often are constructed with fewer layers because of improved waterproofing technology. This could mean flat roofs may not raise the same red flags they used to among prospective homeowners who may want to replace or remodel the roof once they move in.
Prone to water damage or leakage
Many of the potential problems a flat roof may attract – such as water pooling, leakage and resulting rot or damage – are due to poor installation or poor maintenance. Pay careful attention to the roof at the construction phase and throughout its lifecycle to help prevent these problems in the first place.
Parts Of A Flat Roof
To an untrained eye, one flat roof looks very much like another (especially from the ground level!) but, in fact, there are several different flat roof systems to choose from.
At the most basic level, a flat roof consists of three basic components:
- Weatherproofing
- Reinforcement
- Surfacing
Depending on the materials selected, these might be combined into a single product, but all these functions should still be there.
Other Flat Roof Components
Underneath the basics, flat roofs are usually constructed with a ceiling, nailed to joists which support a deck (usually wood in residential construction), a vapor barrier, insulation and a roof board. From there, the flat roof system you choose will determine the materials you apply.
Consider geography, budget and use for the roof to determine the best option.
Warm vs. Cold Roofs
A note to consider before construction: if insulation is installed below the flat roof deck this is called a “cold” roof. Generally, roofers discourage this method for cold climates because it can promote condensation and requires ventilating the roof, which may be difficult to do in small or tight spaces. On the other hand, a “warm” (or hot) roof is one where the insulation is installed above the deck. This situation is suited for cold weather climates. (See more details here).
Here is a diagram of a typical warm roof:
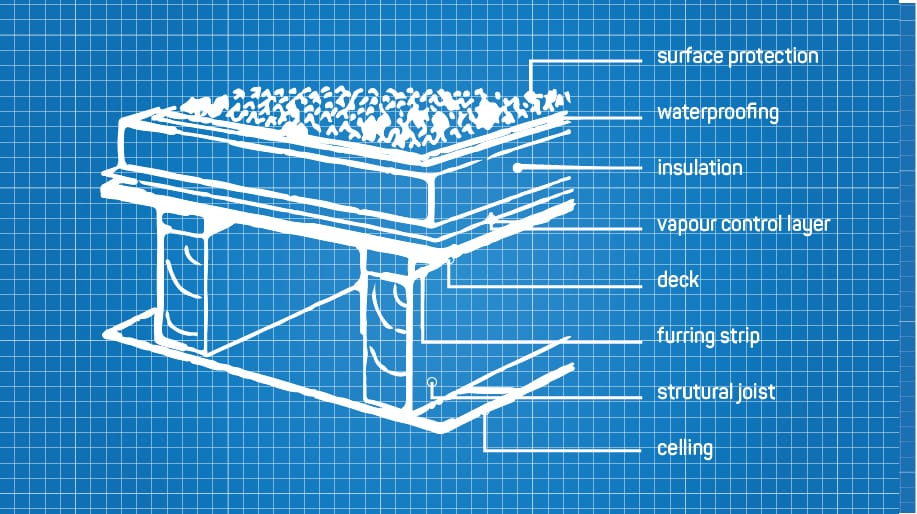
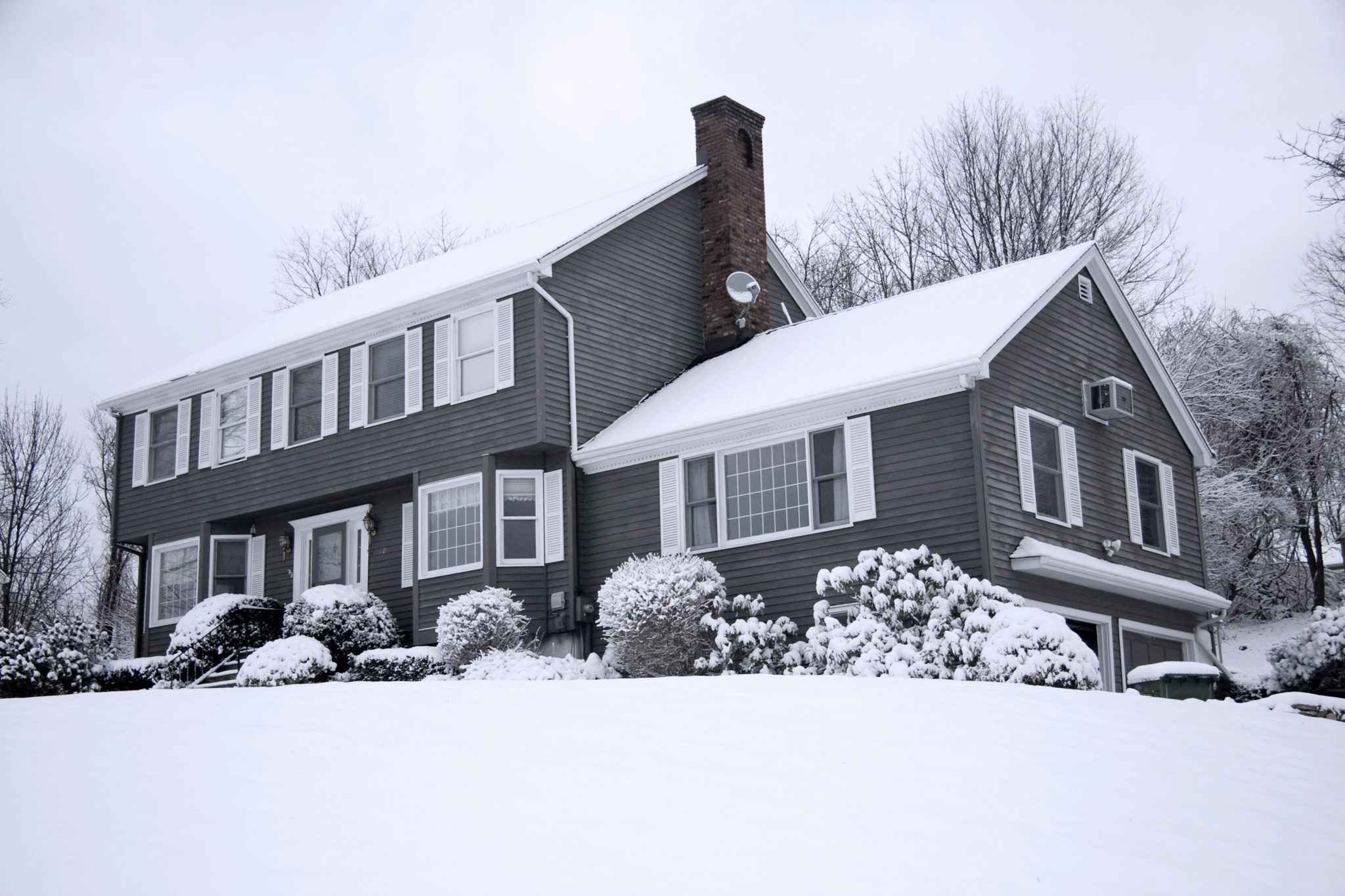
Flat Roof Designs For Houses
There is a wide variety of flat roof materials available, each with its own advantages and drawbacks. The following outlines ways to build, protect and reinforce your roof.
Here we’ll discuss types of flat roofing.
Built Up Roofing (BUR)
This multi-layer roof design is a proven system that has been around for generations. BUR is found in many low slope residential and commercial roofing applications.
MATERIALS
- Alternating layers of roofing felt (usually fiberglass) and hot-applied asphalt
- The final layer of asphalt is topped with gravel or other chipped minerals for several reasons: to protect the asphalt from the sun’s ultraviolet rays, fire proof the material and add weight to secure the roof membrane
- Tried and true for decades
- Considered the most affordable option
- Durable, lasting
- Redundant (if one layer fails there are more layers underneath to provide immediate protection)
- Top layer of light gravel gives an appealing look and reflects the sun
- Hot, messy and slow installation
- Heavy, adds weight to the structure, which must be accommodated
- Difficult to remove
- Difficult to detect and repair leaks due to multiple layers of material
- A layer of roof felt is laid down and hot asphalt is mopped overtop – repeat for two to four layers (called plies)
- Repair involves reapplication of original materials and/or roofing cement to fix cracks or leaks
Single Ply Membranes
In the last 30 to 40 years, these membranes have gained popularity as a single-layer, watertight alternative to traditional built-up flat roofs.
They take less time to apply and although they can be somewhat more expensive, they remain within 10% to 20% of the cost of other methods. Single Ply membranes come in a variety of mil thicknesses, including 45, 60, 80 and 90 mils.
Because they are applied in a single layer on often expansive roofs, they come in large rolls which may require the use of heavy equipment to get the product to the rooftop.
Thermoset (Synthetic Rubber)
MATERIALS
- EPDM (Ethylene Propylene Diene Monomer)
- A flexible synthetic rubber that can be resistant to the sun’s rays (white EPDM) and weathers well against the elements
- Popular and trusted in the commercial market (40% of roofing systems are made with this material)
- Easy to apply
- Hearty and puncture- resistant
- As with all single- ply flat roof membranes, this roofing material doesn’t have the security of extra layers like BUR systems, so extra caution must be paid that the material isn’t punctured or damaged during installation or repair
- There can be some vulnerability where the seams are cemented/taped together
- This is installed by taping or cementing its seams
- It’s secured either mechanically, with adhesive, or using a ballast material (such as paving stones, gravel or green roof vegetation)
Thermoplastic
MATERIALS
- PVC (Polyvinyl chloride)
- Thick and protective, this vinyl product is reinforced with fiberglass or polyester to be long-wearing and resistant to penetration
- It is fire-resistant and UV-resistant
- Contains a lot of chemicals (such as chlorine), making it less popular among builders seeking a greener alternative
- Hot welded or taped at the seams; fastened either mechanically, with adhesive or using ballast
MATERIALS
- TPO (Thermoplastic polyolefin)
- Considered environmentally friendly because it doesn’t contain chlorine
- Flame-retardant and sun-reflecting
- Long-lasting, sturdy and penetration proof
- Because TPO is a newer product, it hasn’t been time-tested over many decades
- Be sure the contractor you hire has sufficient experience with this material
- Sometimes available in peel and stick for easy application; otherwise installed with fasteners and a heat gun
Modified Bitumen (or Polymer Modified Bituminous Materials)
This flat roofing material is popular because it uses trusted weatherproofing materials (asphalt) reinforced with polymers. It has the advantage of multiple layers, but needs fewer layers than built up roofing and is less messy to apply.
MATERIALS
- Waterproofing bitumen is strengthened with polymers (such as atactic polypropylene or styrene butadiene styrene) to add durability and is layered on top of sheets of fiberglass or polyester mats
- Highly puncture- resistant and long lasting
- Affordable
- Comes in smaller-sized rolls than single-ply membranes, making it more manageable to install
- More labor- intensive than single-ply membrane systems because it requires extra layers
- Generally heated by a roofer’s torch to adhere to the roof and seal the seams; may also be applied with cold adhesive
- Newer types are available in “peel and stick” variety
Liquid Applied Roofing
Often called Liquid Roofing, this technology is gaining ground in North America as it becomes more familiar to the industry. Proponents like this product because it’s easy to apply and provides smooth, effective coverage.
MATERIALS
- Waterproofing material made of bitumen and reinforced with glass fibers
- Easy to apply, no heat required
- Liquid creates one monolithic, smooth and effective watertight membrane (no seam adhesion required)
- Highly resistant to sun’s UV rays and heat
- Dries rapidly
- May require finding a specialized contractor experienced with its application
- A first layer of liquid cold-poured on top of insulation, with a second layer applied on top of reinforcing asphalt or felt
Spray On Roofing
Often called Liquid Roofing, this technology is gaining ground in North America as it becomes more familiar to the industry. Proponents like this product because it’s easy to apply and provides smooth, effective coverage.
MATERIALS
- A sun-reflective protective coating made of silicone, acrylic or aluminum
- Easy to apply
- Creates an effective weatherproof, fire-resistant and UV-reflective barrier
- Because it’s sprayed on, creates a seamless layer
- Expensive
- May require searching for specialized contractor who is experienced with its application
- Sprayed directly over insulation
Metal Roofing
Metal is an expensive, but stylish option because it is straightforward, unique and non-chemical.
MATERIALS
- Large panels of standing seam steel, aluminum, zinc or copper
- Long-lasting
- Easy to install
- Acts as both waterproofing and sun/fire protection for the roof (no top layer required)
- Easy to maintain
- Made of recycled materials (which can again be recycled after use)
- High cost of materials
- Can be noisy during a rain event.
- Hail can create a great deal of damage to the roof surface.
- Installed over insulation
- Repaired using soldering (for aluminum, use fiberglass patches or aluminized caulking)
Can you have a flat roof with shingles?
Roofing experts discourage the use of shingles on a flat roof. As few points of sealing as possible will reduce potential for leakage. This is why most flat roofs use large squares or single sheets of materials. In some cases, a homeowner may choose an option such as a Self-Adhering Membrane Residential Roof System, which offers the multi-layer protection of a membrane roof, with the traditional granule look of a shingled or built-up roof. These offer lasting protection against snow, ice and elements – and hold up well to foot traffic on low-slope roofs. They’re peel-and-stick cold application, and availability in single, double or triple layer reinforcement make them a popular choice for roofs with at least 1:12 slope.
How to Make a Flat Roof Last
It is incumbent upon the owner of a flat roof to regularly inspect and maintain the roof. This will make a significant difference in maintaining its integrity and longevity.
A basic inspection is suggested twice a year and after any major rain storms. We recommend consulting a roofing professional who is fully versed in rooftop safety techniques and precautions.
Flat Roof inspection checklist:
- In normal circumstances, wait until 48 hours after a rainfall to clean and inspect the roof. Any water should have evaporated by this time. If it hasn’t, that’s a sign of a problem with roof drain parts or the drainage system.
- To help see where any water might be collecting, clean any debris from the flat roof surface, including sweeping or gathering fallen leaves or branches and clearing any loose debris or gravel that may block drainage holes.
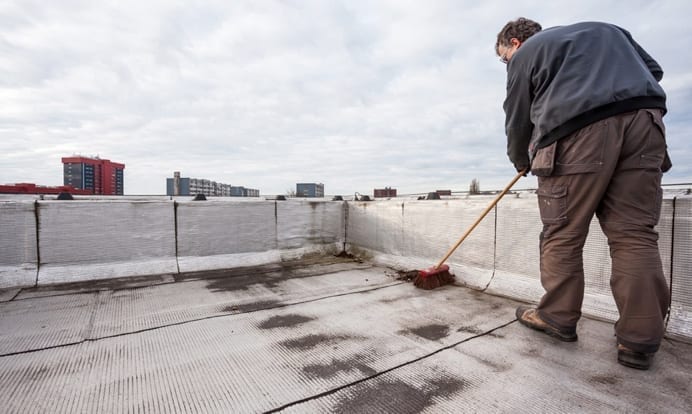
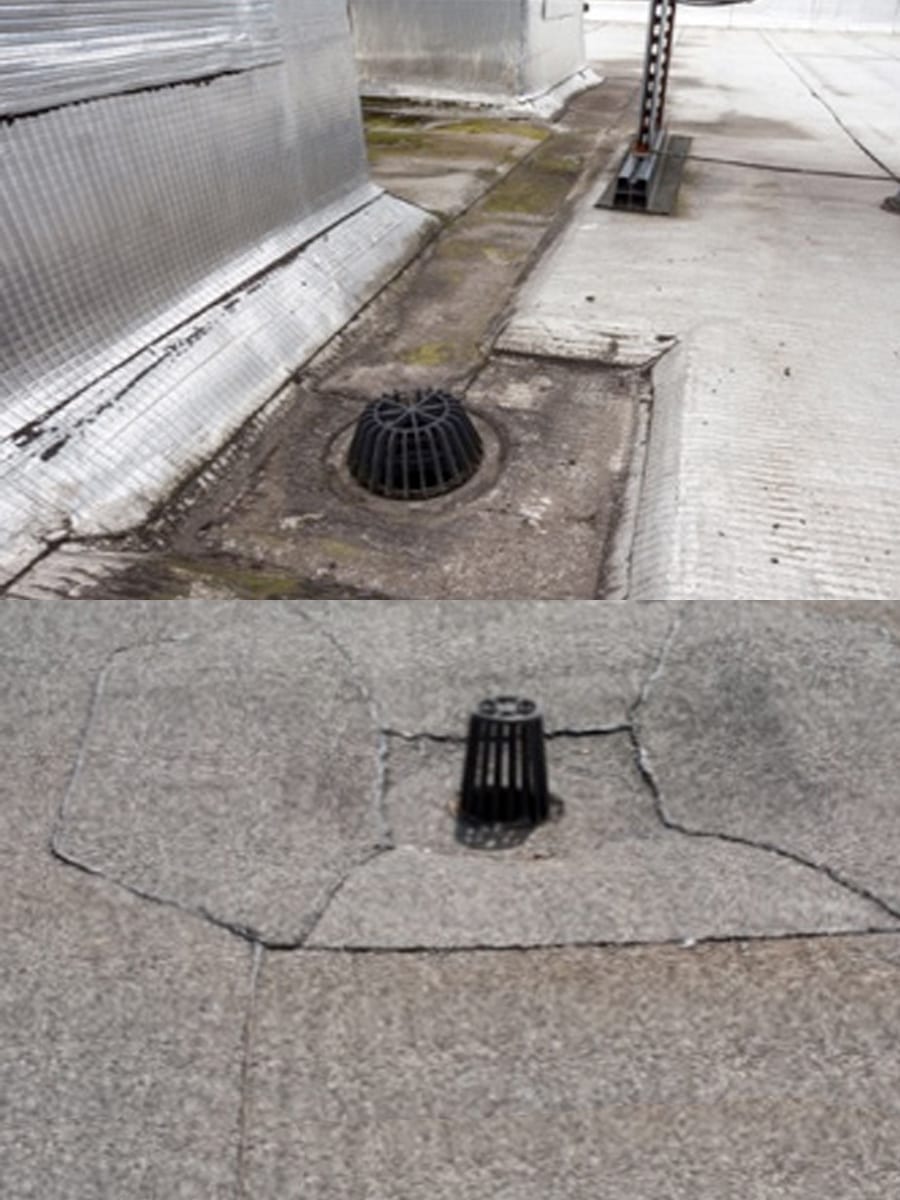
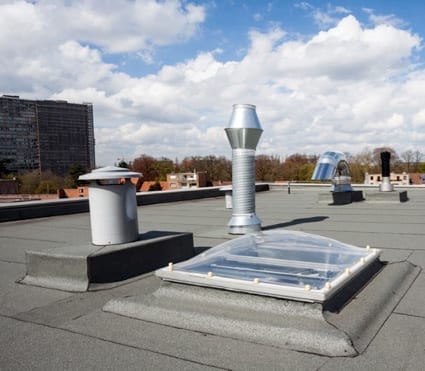
- Inspect flashings around the chimney and skylights. If the flashing material is cracked or rusty, you will want to have it repaired as soon as possible.
- Inspect the integrity of the top layer of protection (often a gravel or chipped mineral mixture) to ensure it hasn’t dispersed and left a bald patch. This is key to protecting the membrane underneath while also providing sun and fire protection. On a built-up roof, when gravel becomes sparse, the asphalt layer underneath can dry and crack under the sun. This could lead to “alligatoring,” which may eventually cause the layer to leak and fail.
- Check for any damage, puncturing, rips or wrinkling of the membranes. This might be difficult to see if a layer of chipped material or gravel is on top. Regardless of your flat roof design, take time to thoroughly check the surface for flaws.
- Any damage should be repaired immediately to return watertight protection to the roof and prevent further deterioration.
- If the top layer of gravel needs to be replaced or replenished, consult a roofing professional for proper application over the surface of the roofing material.
(Source: CAA Quebec.)
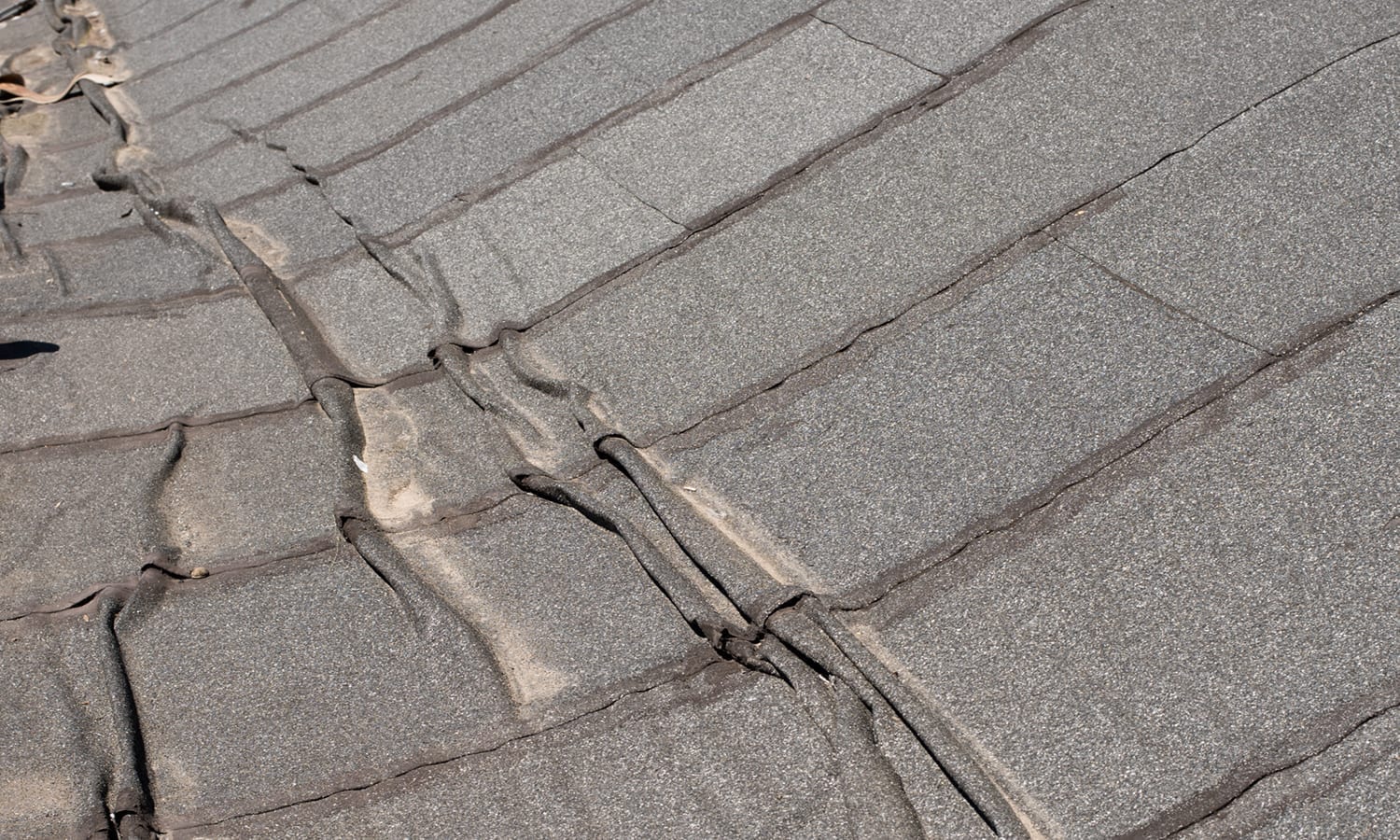
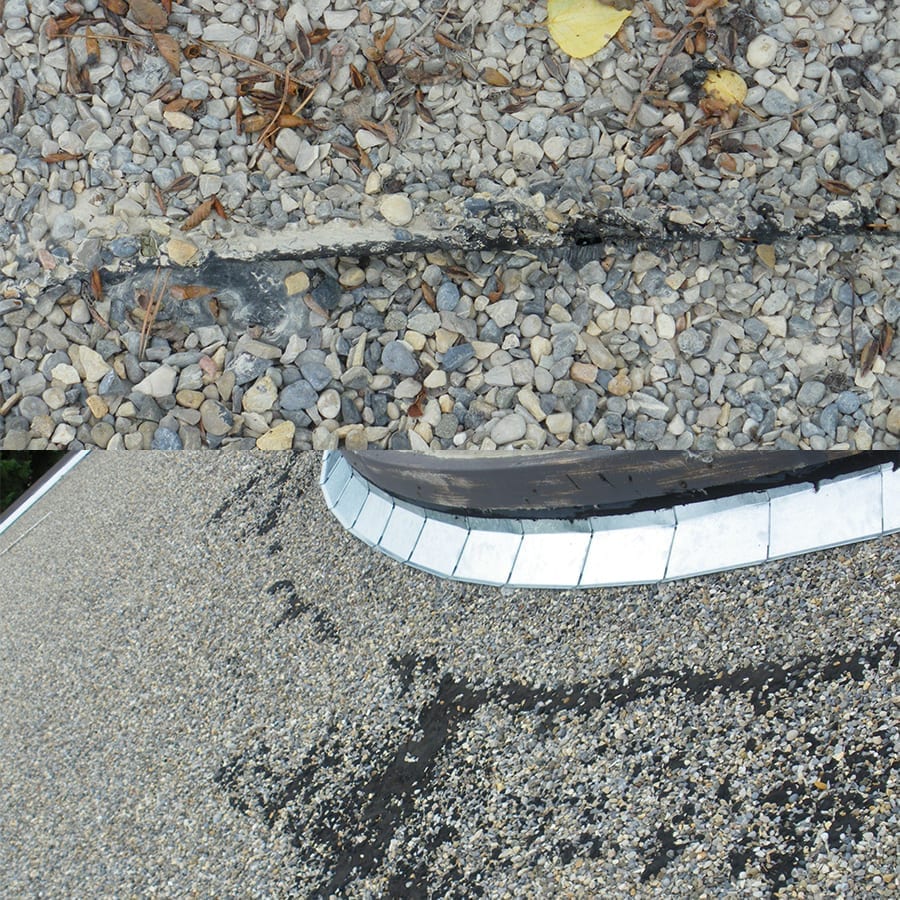
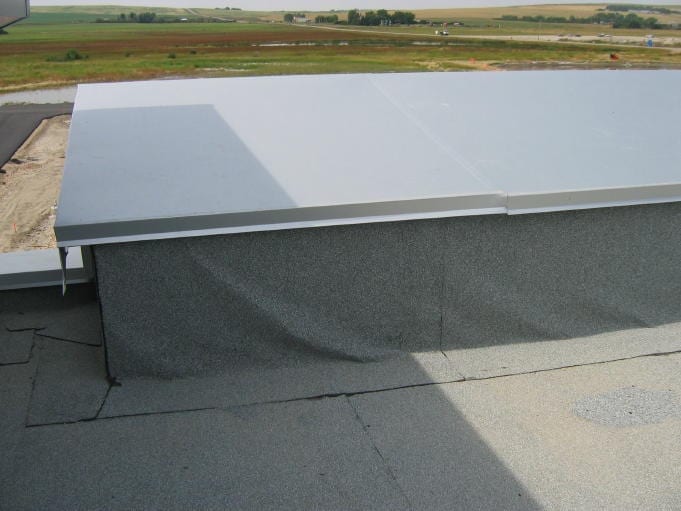
A crowning feature
Education is the key to choosing a flat roof that fits your budget, style and geography.
Regardless of the type of roof selected, with an experienced contractor and a solid understanding of materials and maintenance, you’ll be well on your way to constructing a protective, lasting feature for your home.
Transitioning from a flat roof to a shingle roof requires special attention. Read more in our article on how to join a flat roof to a shingle roof.