L’histoire des bardeaux d’asphalte
Qui a inventé le bardeau d’asphalte? Techniquement, il s’agit de Henry Reynolds, de Grand Rapids au Michigan. Il a pris un rouleau de matériau de couverture et l’a découpé en bardeaux en 1903. Cependant, l’histoire des bardeaux d’asphalte n’est pas l’œuvre d’une seule personne. Au contraire, une série de couvreurs, de fabricants et d’organisations externes ont tous contribué au développement du bardeau d’asphalte tel que nous le connaissons aujourd’hui. Ils ont tous essayé d’améliorer les matériaux de couverture pour résister à la pluie, au vent, à la grêle et à d’autres menaces environnementales.
Pour bien comprendre les évolutions majeures qui ont fait des bardeaux d’asphalte l’un des matériaux de construction les plus populaires de tous les temps, il faut remonter aux années 1800.
Les toitures avant les bardeaux d’asphalte
Dans l’Amérique des années 1800, les toitures ressemblaient beaucoup à celles des siècles précédents. Il existait quelques matériaux différents pour la couverture des maisons : bardeaux de bois, tuiles d’argile, ardoises et métal. Aujourd’hui, on peut encore voir ces matériaux de couverture sur des maisons historiques. À l’époque, la disponibilité et le coût des matériaux déterminaient ce que chaque propriétaire pouvait avoir sur son toit. En fait, les maisons des quartiers pauvres pouvaient encore être couvertes de chaume, un matériau à base de paille ou de foin que l’on trouve sur de nombreux toits anciens.
Cependant, dans les années 1840, Samuel M. et Cyrus M. Warren, de Cincinnati, ont commencé à utiliser un tissu en coton pour la toiture. Ils ont utilisé le tissu comme base ou « nappe » du matériau de couverture. Ils ont enduit la nappe de goudron de pin et ont saupoudré du sable dessus. Ce matériau offrait une certaine protection contre l’humidité et s’est rapidement imposé. Pour améliorer leur produit, les frères Warren sont passés au goudron de houille, qui était moins cher que le goudron de pin.
Bien plus tard, dans les années 1860, les conditions du marché ont à nouveau changé, le goudron de houille devenant une option coûteuse. Les frères Warren ont découvert que la nouvelle industrie pétrolière produisait de l’asphalte, un matériau utile à leurs fins. Ils ont donc commencé à utiliser l’asphalte pour enduire le tissu. Ils ont également remplacé le sable par des granulés d’ardoise.
Ce n’est qu’en 1903 que Henry Reynolds a commencé à découper ce matériau en bardeaux individuels. Ce faisant, il a facilité l’application et amélioré l’aspect du toit. Comme pour beaucoup d’inventions précoces, d’autres entreprises et personnes ont prétendu fabriquer des bardeaux à la même époque.
La popularité croissante des bardeaux d’asphalte
De nombreux couvreurs ont commencé à découper ces premiers rouleaux de toiture en bardeaux. Puis, en 1911, aux États-Unis, le NBFU (National Board of Fire Underwriters) a cherché à sensibiliser les gens au fait que les bardeaux de bois présentaient des risques d’incendie importants. Les bardeaux d’asphalte constituaient une excellente option de remplacement qui réduisait considérablement les risques d’incendie.
D’autres couvreurs ont commencé à découper des bardeaux dans le matériau en rouleau à l’aide de matrices à rouleaux pour copier Reynolds. Les progrès technologiques des machines de fabrication ont contribué à réduire les coûts et ont permis aux couvreurs de répondre à la demande de ces nouveaux bardeaux. Ensuite, les fabricants de toitures ont suivi la tendance des bardeaux. Dans les années 1920, l’entreprise Bird & Son a proposé les premiers bardeaux en bande. Elle les a appelés Neponset Twin Shingles et s’est vantée que le produit présentait des coûts d’installation réduits et moins de fissures et de trous de clous. Il imitait également l’aspect des toitures en ardoise.
Ces bardeaux n’étaient disponibles qu’en rouge « tendre » et en vert. Il s’agissait des couleurs naturelles de l’ardoise disponible localement que Bird & Son écrasait et ajoutait sur le dessus des bardeaux. Le rouge et le vert sont restés le seul choix de couleur jusqu’à ce que les marques de bardeaux proposent des granules de céramique pouvant être de n’importe quelle couleur. Si les fabricants n’utilisaient qu’une seule teinte d’ardoise, les différences de teinte naturelle du matériau seraient perceptibles et donneraient un aspect incohérent aux bardeaux. Pour masquer ces variations de teinte, les fabricants mélangeaient différentes couleurs de granules. Par exemple, ils mélangeaient des granules de différentes teintes de rouge pour créer un bardeau rouge d’apparence plus uniforme. Cette tendance s’est poursuivie pour les granules de bardeaux en céramique, qui ont été conçus plus tard.
Les fabricants ont créé la sensation de profondeur et de dimension sur les bardeaux avec ces granules. Plus précisément, une bande de granulés foncés (noirs) était déposée pendant le processus de fabrication des bardeaux dans la zone du bardeau qui se trouverait immédiatement sous le bord inférieur du bardeau sus-jacent une fois installé sur le toit. Cette « bande d’ombre » sombre convainc l’œil humain que le bardeau est assez épais, car elle semble projeter une ombre sur le bardeau du dessous. Ces dernières années, les bandes d’ombre ont eu tendance à être plus subtiles (utilisant souvent des granules qui ne sont pas d’un noir pur). Les bandes d’ombre d’un noir pur étaient considérées par certains comme trop évidentes. Une autre préoccupation était que si la largeur de la bande de granules foncés variait légèrement, ce qui se produisait souvent dans le processus normal de fabrication des bardeaux, l’aspect général du toit paraissait étrange et incohérent. Des bandes d’ombre plus subtiles ont réduit ce risque esthétique.
Les premiers bardeaux étaient également posés différemment des bardeaux d’aujourd’hui. Dans les années 1920 et 1930, les bardeaux étaient des pièces uniques, carrées ou rectangulaires. S’il existait d’autres formes sur le marché européen, les bardeaux américains étaient le plus souvent « droits » ou rectangulaires. Ils étaient généralement posés en ligne droite. Certains étaient posés à la manière hollandaise, ce qui impliquait un pureau de bardeau plus important et un chevauchement horizontal supplémentaire entre les bardeaux.
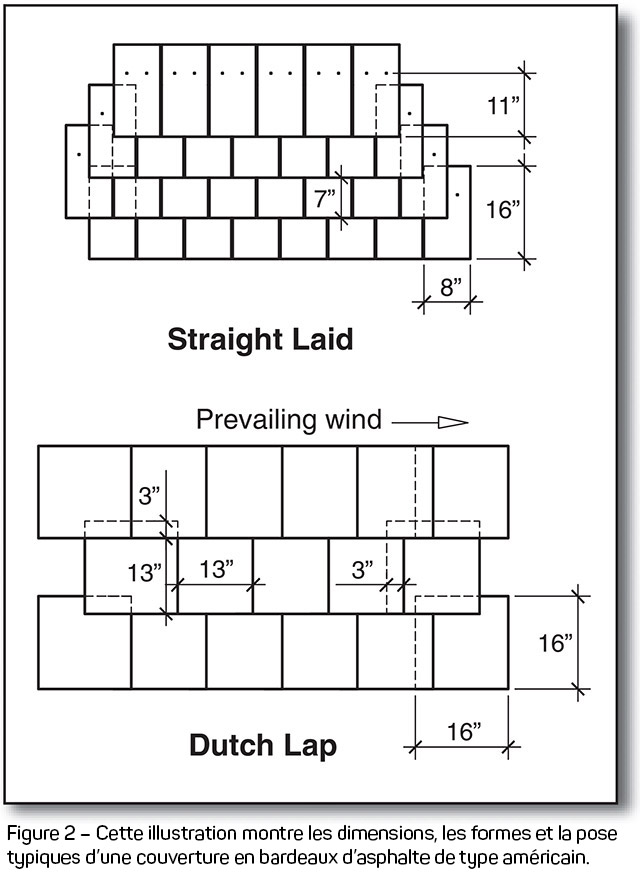
En 1935, les premiers bardeaux à trois pattes ont été produits. Ils étaient la norme de l’industrie : 12 pouces sur 36 pouces. Ils étaient posés en style droit, se chevauchant verticalement, mais pas horizontalement, tout comme aujourd’hui. Dans les années 1950, cette taille est devenue la norme chez la plupart des fabricants de bardeaux.
Puis, dans les années 1970, le Canada a adopté le système métrique. IKO a commencé à offrir des bardeaux plus grands à cette époque. L’innovant « bardeau métrique » mesure 13 pouces 1/4 de largeur sur 39 pouces 3/8 de long. Ce sont des dimensions inhabituelles en système impérial, mais en système métrique, le bardeau fait tout simplement 337 mm sur 1 000 mm. Grâce à ces bardeaux plus grands, les couvreurs ont besoin de moins de bardeaux par carré de toiture. En outre, ces bardeaux ont un impact visuel plus important et sont plus rapides à poser pour les couvreurs.
La popularité des bardeaux a continué de croître en Amérique du Nord au cours des décennies suivantes. En 1939, on comptait 32 fabricants qui produisaient 11 millions de carrés de bardeaux.
Les matériaux des premiers bardeaux
Les premiers bardeaux avaient les trois mêmes composants qu’aujourd’hui : un matériau de renforcement de base appelé nappe, de l’asphalte et un revêtement supérieur en granules minéraux. Cependant, chaque matériau utilisé pour ce composant a changé au fil du temps pour offrir de meilleures performances et une plus grande sécurité au toit.
Par exemple, dans les années 1940, l’industrie de la toiture s’est éloignée des nappes de chiffon en coton par lesquelles les frères Warren avaient commencé. Au lieu de cela, les fabricants de bardeaux ont commencé à utiliser un matériau organique très résistant comme base pour les bardeaux. La nappe organique était saturée d’un asphalte souple « saturant » et enduite sur le dessus et le dessous plus dur d’un asphalte résistant aux intempéries.
Puis, dans les années 1970 et 1980, certains fabricants de bardeaux sont passés à la fibre de verre inorganique pour la nappe de bardeaux. La fibre de verre était plus fine, mais plus solide, et pesait moins que les nappes organiques. Contrairement aux nappes organiques, les nappes en fibre de verre ne nécessitaient pas l’asphalte saturé particulier utilisé sur les nappes organiques, car les nappes sont intrinsèquement résistantes à l’absorption d’humidité. En outre, les bardeaux d’asphalte fabriqués à l’aide de nappes de fibre de verre sont également plus résistants au feu. Tous les fabricants de bardeaux ont rapidement suivi cette tendance, et les nappes en fibre de verre sont désormais la norme dans l’industrie.
Les matériaux dont sont faits les bardeaux continuent d’être améliorés à ce jour.
Bardeaux laminés multicouches
Avant les années 1970, presque tous les bardeaux étaient découpés à partir d’une seule couche de matériau de couverture. Au cours du processus de fabrication, on versait des granulés colorés dans l’asphalte chaud de différentes zones de la toile de couverture, et des rouleaux de pression étaient utilisés pour noyer les granulés dans l’asphalte avant qu’il ne refroidisse. Le processus de fabrication a permis une transition graduelle de la couleur d’une zone de granules à l’autre. De nombreux propriétaires se sont habitués à ces mélanges de couleurs plus douces de bardeaux, avec des transitions discrètes entre les zones claires et foncées des bardeaux. Dans les années 1970, les goûts plus modernes exigeaient une transition plus nette entre les couleurs. Pour y parvenir, les bardeaux laminés ont été introduits.
Pour fabriquer des bardeaux laminés, deux couches de matériau sont collées ensemble. On trouve une couche supérieure « dentée » de feuille de toiture et une couche inférieure « de cale continue ». Les couleurs des granules de la couche dentée ne sont pas susceptibles de coïncider exactement avec celles des granules de la couche de cale. Il en résulte une coloration plus contrastée et plus nette des bardeaux, et une fois qu’ils sont installés sur le toit, ces bardeaux laminés ressemblent davantage à une ardoise, une tuile ou un bardeau de bois.
Les propriétaires ont rapidement apprécié cette amélioration esthétique des bardeaux d’asphalte laminés. Les entrepreneurs en couverture ont également tiré un avantage de ces nouveaux bardeaux. Les bardeaux à trois pattes nécessitaient une attention et des mesures supplémentaires pour aligner les bardeaux correctement et créer l’aspect « brique ». Bien que les bardeaux laminés requièrent également des mesures précises de décalage et de pureau des bardeaux, l’aspect multicouche aléatoire des bardeaux laminés modernes offre une plus grande tolérance pour les ajustements mineurs du toit; et donc, la pose est plus simple dans une certaine mesure.
À l’origine, les fabricants fabriquaient les bardeaux laminés par un processus discontinu « hors chaîne »; mais, grâce aux progrès des équipements de fabrication, le processus est désormais continu. Des rubans de dents et de matériaux de calage sont coupés, superposés et laminés ensemble. Ensuite, une machine découpe le matériau combiné en longueurs de bardeaux individuels. Au fil des ans, les fabricants ont également introduit de nombreux motifs de coupe créatifs, des mélanges de couleurs, des bandes d’ombre et même une troisième couche pour certains bardeaux laminés.
Défis environnementaux
Les bardeaux d’asphalte offraient de nombreuses caractéristiques souhaitables que les propriétaires pouvaient apprécier, de l’imperméabilité à la beauté et à la résistance au feu. Cependant, au milieu du 20e siècle, la dégradation des conditions météorologiques constituait encore un défi important à relever pour l’industrie de la couverture.
L’un des principaux problèmes des premiers bardeaux était leur capacité à résister aux vents violents.
Avant les années 1950, les bardeaux d’asphalte étaient souvent collés manuellement avec des adhésifs bitumineux pour les aider à résister au soulèvement par le vent. À la fin des années 1950, les fabricants ont créé des bardeaux autoadhésifs. À l’usine de fabrication, des bandes d’asphalte adhésif étaient appliquées directement sur la surface des bardeaux. Cette innovation a permis aux installateurs de toitures d’économiser du temps, de réduire le désordre et les frais liés à l’application d’adhésifs sur site. Après avoir été exposés au soleil, ces bardeaux autoadhésifs collaient aux bardeaux de la rangée adjacente et pouvaient mieux résister aux forces du vent.
Les fabricants ont continué à améliorer les adhésifs qu’ils utilisent pour les bardeaux. Les premiers adhésifs étaient basés sur des résines d’asphalte plus dures; mais, avec l’avènement des bardeaux en fibre de verre, on a découvert un mastic plus solide et plus « collant », utilisant de l’asphalte combiné à des polymères sélectionnés, qui offre une meilleure résistance aux vents violents.
La grêle est un autre problème auquel le toit en bardeaux d’une maison doit faire face. Dans les années 1960, l’industrie des assurances s’est de plus en plus préoccupée de la performance des toits pendant les tempêtes de grêle. UL (Laboratoires des assureurs), IBHS (Insurance Institute for Business & Home Safety) et d’autres membres de l’industrie de la toiture ont créé un système de classification de la résistance aux impacts pour les matériaux de couverture, y compris les bardeaux d’asphalte.
Aujourd’hui, il existe deux tests d’impact courants dans l’industrie. L’un est le test UL 2218, qui utilise des billes d’acier lâchées d’une certaine hauteur sur une plateforme d’essai de bardeaux. L’autre est le test de la mutuelle des manufacturiers, FM 4473, qui consiste à lancer des boules de glace de différents diamètres sur des plateaux d’essai de bardeaux. Les deux méthodes d’essai donnent un système à quatre classes, les bardeaux de classe 4 étant les plus résistants aux chocs.
Les tests de résistance au vent des bardeaux d’asphalte ont également évolué au cours des trois ou quatre dernières décennies. À l’origine, le seul test industriel permettant d’évaluer la résistance au vent était réalisé par ASTM International et demandait une plateforme de bardeaux d’asphalte, installée selon les instructions du fabricant et conditionnée dans un grand four pour permettre à la colle autoadhésive de s’activer. La plateforme était ensuite placée devant un grand ventilateur, qui soufflait de l’air (vent) sur la plateforme.
Ce test intuitif de résistance au vent induit par un ventilateur existe toujours aujourd’hui (ASTM D3161), mais l’industrie a utilisé des principes d’ingénierie scientifique avancés pour évaluer la résistance inhérente au soulèvement des bardeaux (ASTM D6381) et la force d’adhérence de l’adhésif plus précisément. L’évaluation conjointe de ces deux propriétés des bardeaux permet de déterminer la résistance théorique globale au vent d’un système de toiture installé (ASTM D7158). La méthode d’essai donne lieu à une échelle de classement, la classification la plus élevée étant la classe H, ce qui correspond à une vitesse du vent sur le toit estimée à 150 mi/h (241 km/h).
L’avenir des toitures en asphalte
Jusqu’à présent, l’histoire des bardeaux d’asphalte est celle d’une élaboration à long terme et d’une réponse aux besoins des consommateurs et aux défis environnementaux. En se tournant vers l’avenir, les fabricants de toitures mettent au point des bardeaux haute performance qui peuvent contribuer à relever les défis auxquels nous devons faire face en raison du changement climatique.